Centre for Waste-to-Energy (CWE)
at Saint-Ouen-sur-Seine
Syctom
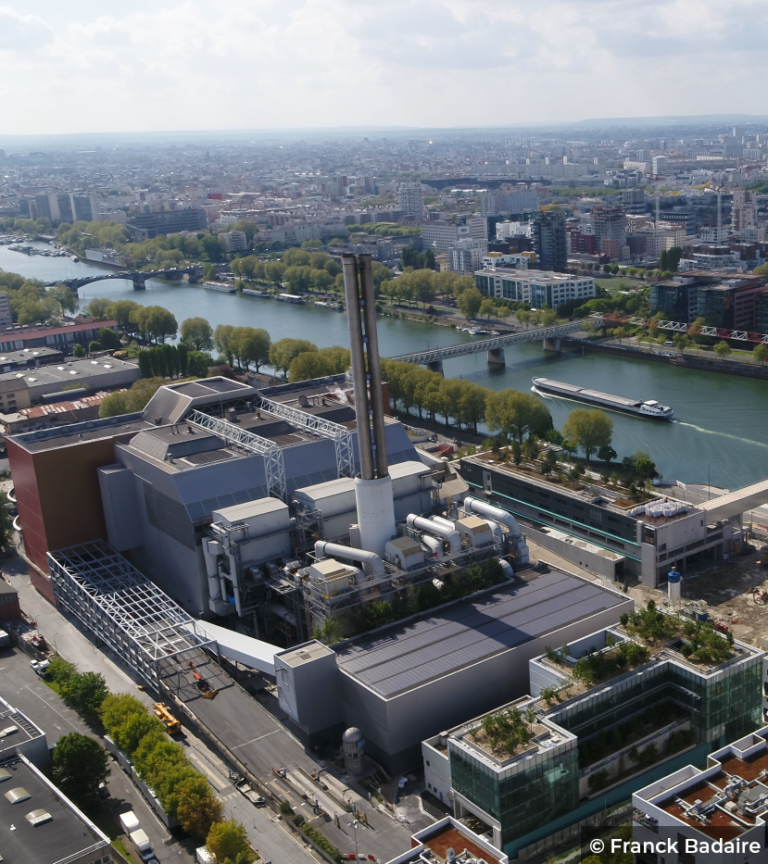
The Centre for Waste-to-Energy at Saint-Ouen-sur-Seine, Syctom’s second industrial site, was commissioned in 1990 within an industrial environment. The facility receives, treats and incinerates household waste from Audon residents and 16 other neighbouring municipalities that are Syctom members. The heat generated by the waste is used to produce steam to supply the Parisian Urban Heating Company (CPCU, Compagnie Parisienne de Chauffage Urbain) heating network, and electricity to run the centre, the excess of which is sold to EDF. Waste collected from almost 1.5 million residents is incinerated, producing heat for around 110,000 housing equivalents and almost 57,000 MWh of electricity (around 80% of which is for self-consumption). Since 2015, work has been underway to modernise the process for treating fumes (under the project management of setec énergie environnement / Ingevalor) and industrial effluents, in order to significantly optimise energy efficiency and environmental performance. At the same time, Syctom is carrying out an ambitious urban integration project.
Setec énergie environnement has developed solutions to improve the plant’s energy efficiency. By including a system for recuperating latent energy from fumes to heat water from the Seine, which CPCU uses in its process as a substitute for fossil fuels. The ORC (Organic Rankine Cycle) turbines will also generate additional electricity.
Syctom has entrusted setec énergie environnement / Ingevalor with the task of designing, building and commissioning the plant’s three dry fumes treatment lines, without disrupting operations. In addition to the expertise in the treatment of incineration fumes and the management of works on operating sites, the consortium brings to Syctom its experience in energy recuperation from incineration fumes.
Innovative solutions such as combined heat and power (CHP) using ORC turbines, optimised steam production and the capture of waste energy by condensing fumes for use in the CPCU’s heating networks are being implemented to optimise the site’s over-all efficiency and decarbonisation, making the Saint Ouen site the most efficient incineration plant in France.
Meanwhile, as part of another project, setec énergie environnement has also coordinated an international research consortium to work on a CO² capture project involving the installation of a test facility.
Cogeneration using an ORC turbine, optimisation of steam production, capture of waste energy by condensation of fumes with a view to reuse in the CPCU heating networks and a project to set up a CO² capture pilot are some of the innovative solutions being implemented.


Syctom has entrusted setec énergie environnement / Ingevalor with the task of designing, building and commissioning the plant’s three dry fumes treatment lines, without disrupting operations. In addition to the expertise in the treatment of incineration fumes and the management of works on operating sites, the consortium brings to Syctom its experience in energy recuperation from incineration fumes.
Innovative solutions such as combined heat and power (CHP) using ORC turbines, optimised steam production and the capture of waste energy by condensing fumes for use in the CPCU’s heating networks are being implemented to optimise the site’s over-all efficiency and decarbonisation, making the Saint Ouen site the most efficient incineration plant in France.
Meanwhile, as part of another project, setec énergie environnement has also coordinated an international research consortium to work on a CO² capture project involving the installation of a test facility.
Cogeneration using an ORC turbine, optimisation of steam production, capture of waste energy by condensation of fumes with a view to reuse in the CPCU heating networks and a project to set up a CO² capture pilot are some of the innovative solutions being implemented.
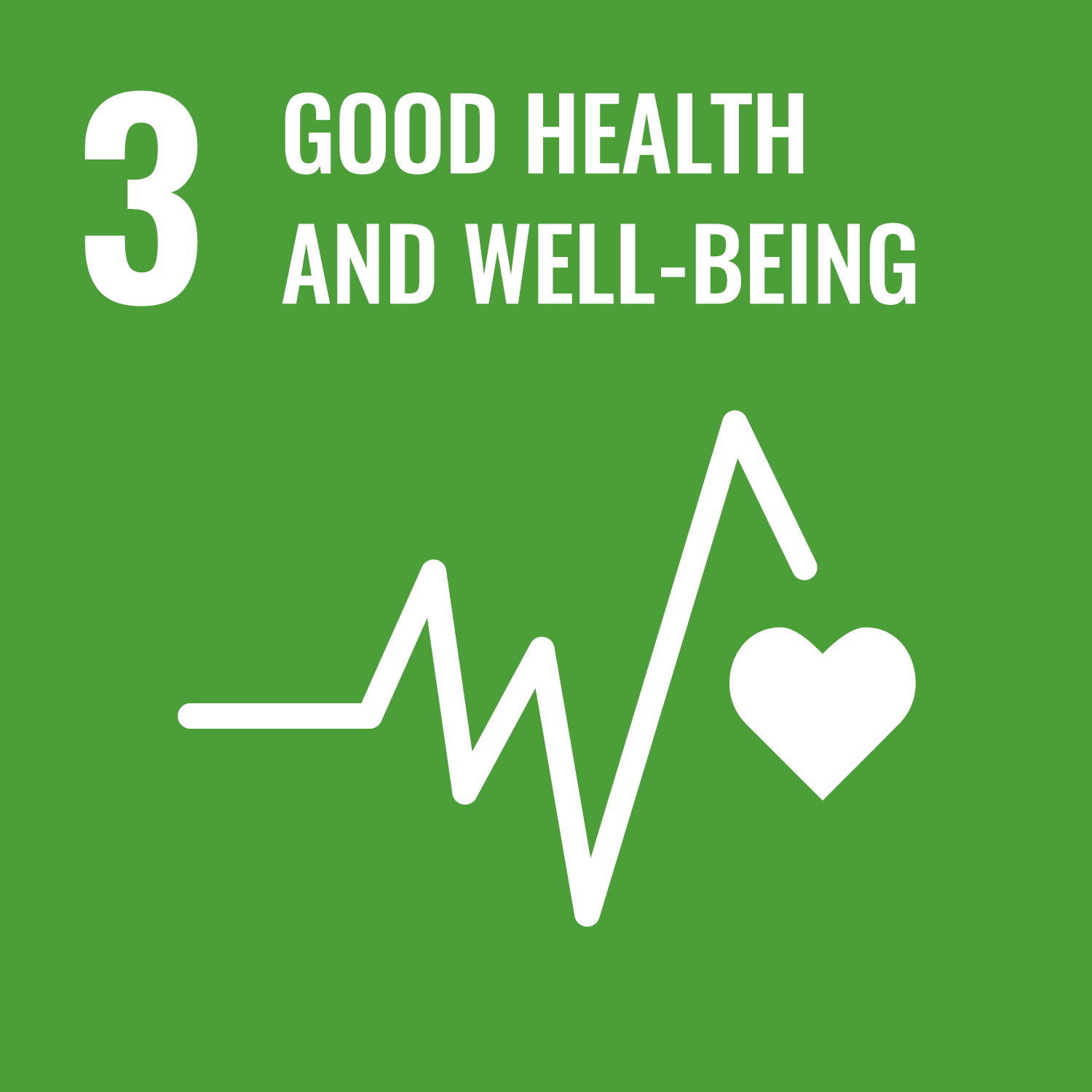
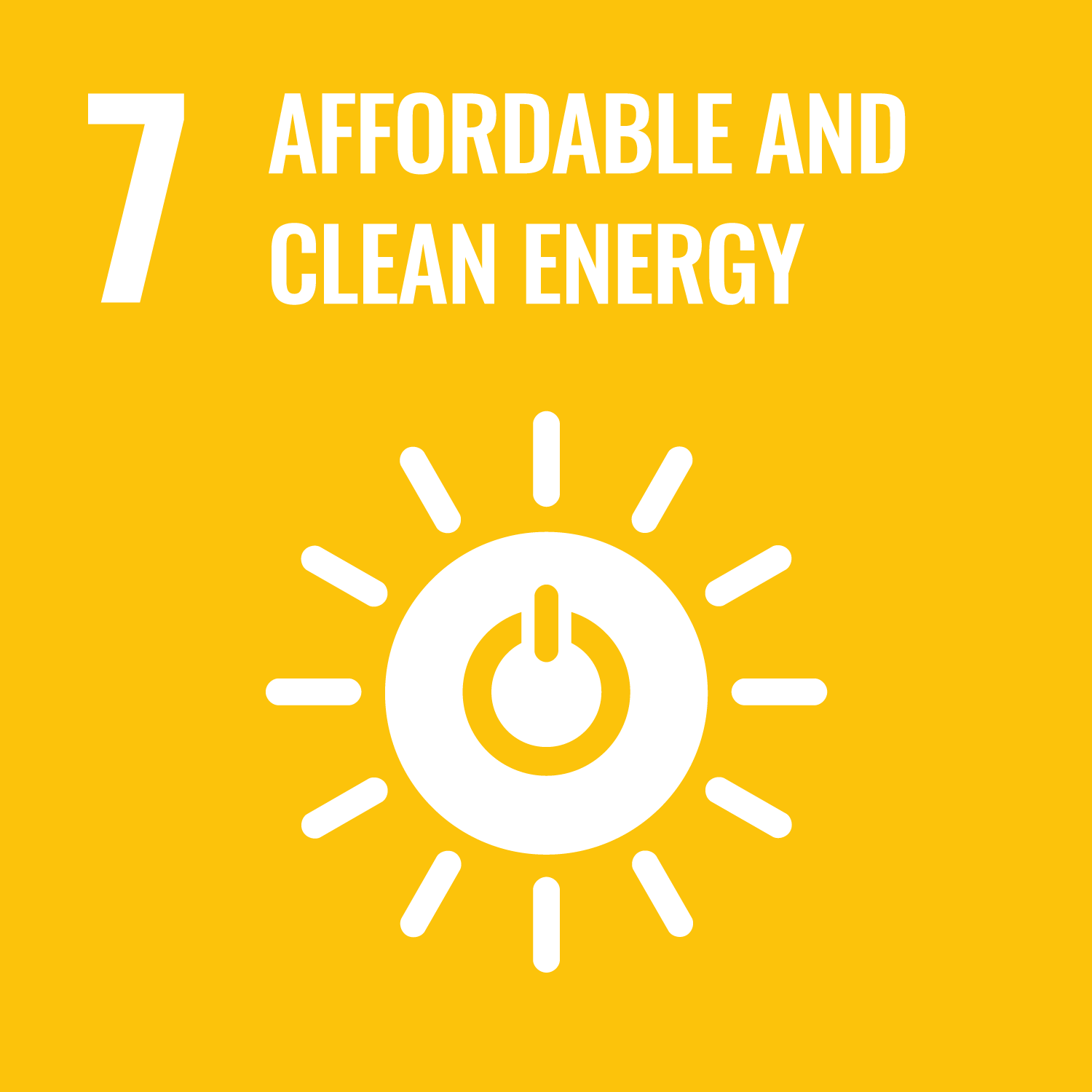
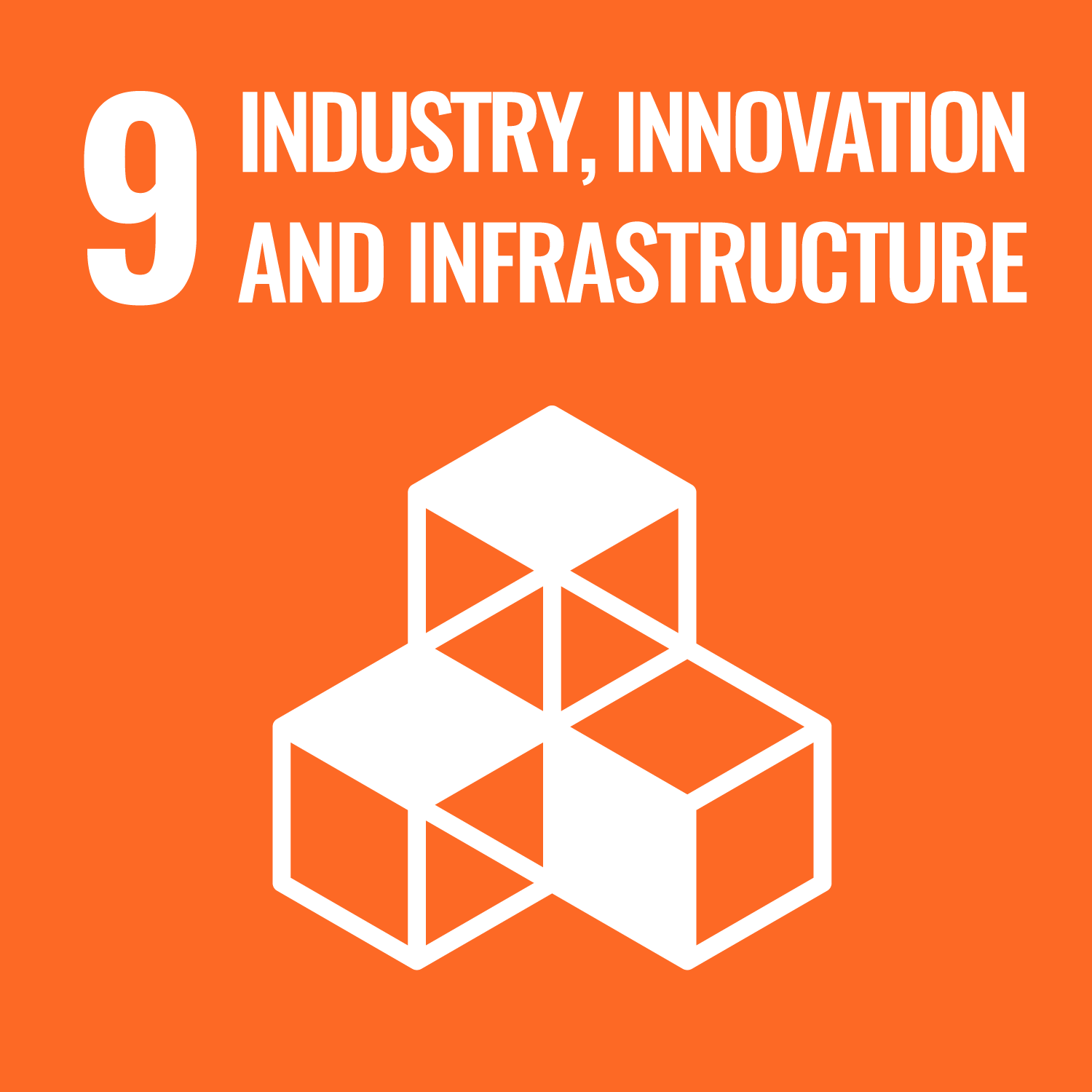
It would be impossible to shut down the plant and process the annual 600,000 tonnes of waste elsewhere. The works are therefore being carried out with two of the three sections in operation. This leads to considerable restrictions due to coactivity on and around the site. We need to be extremely attentive to keep to schedules, but also reactive and flexible to adapt to the life of construction sites and the many companies involved.
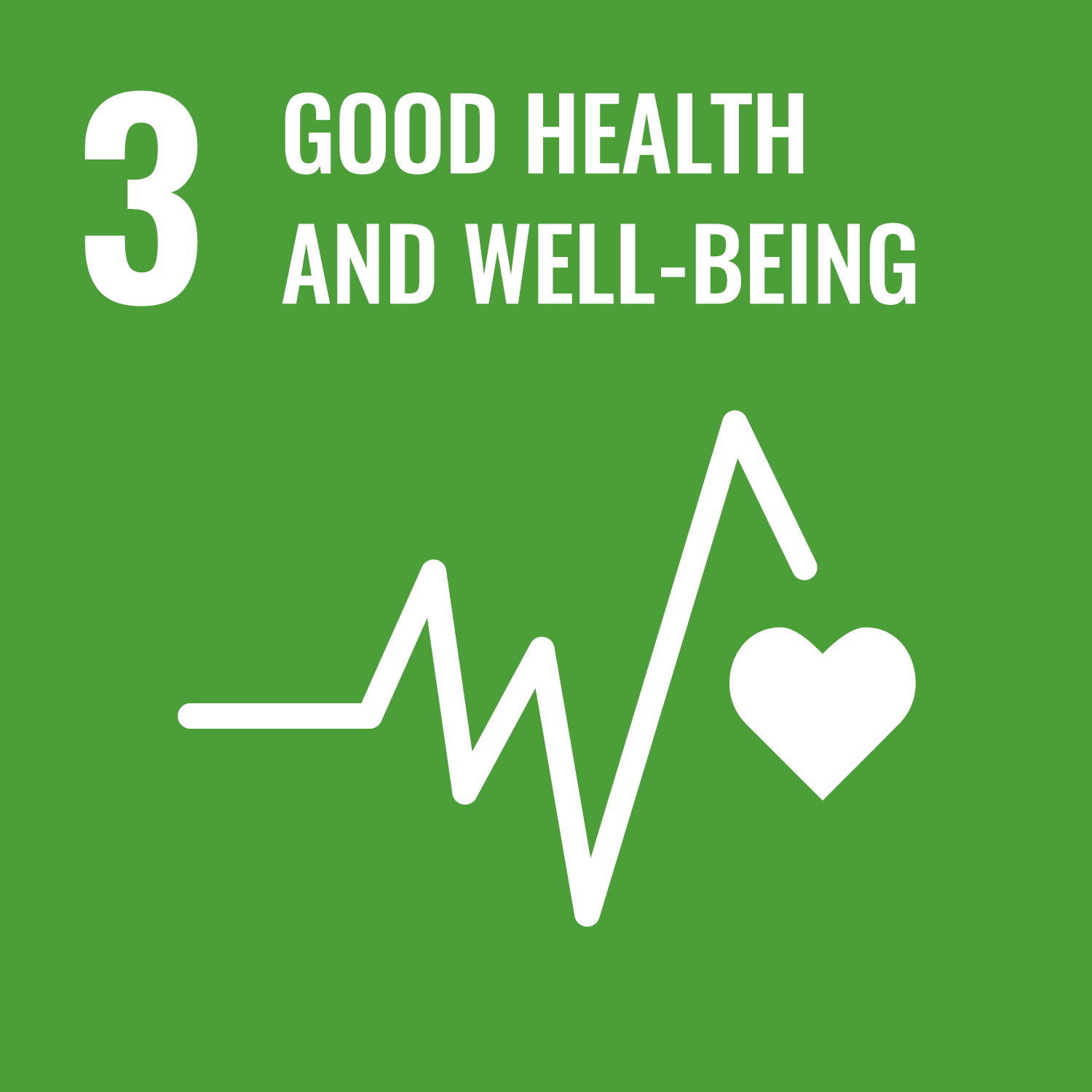
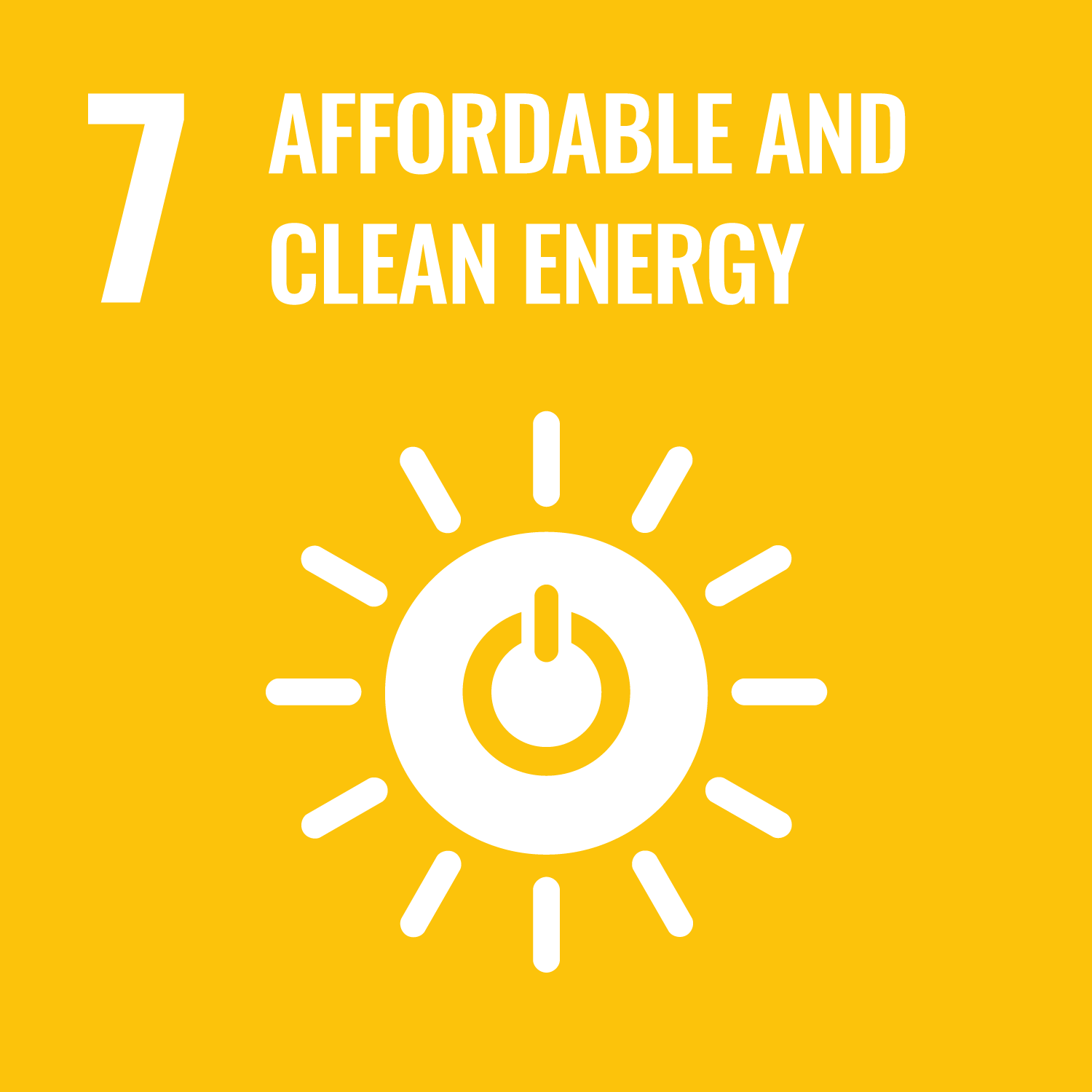
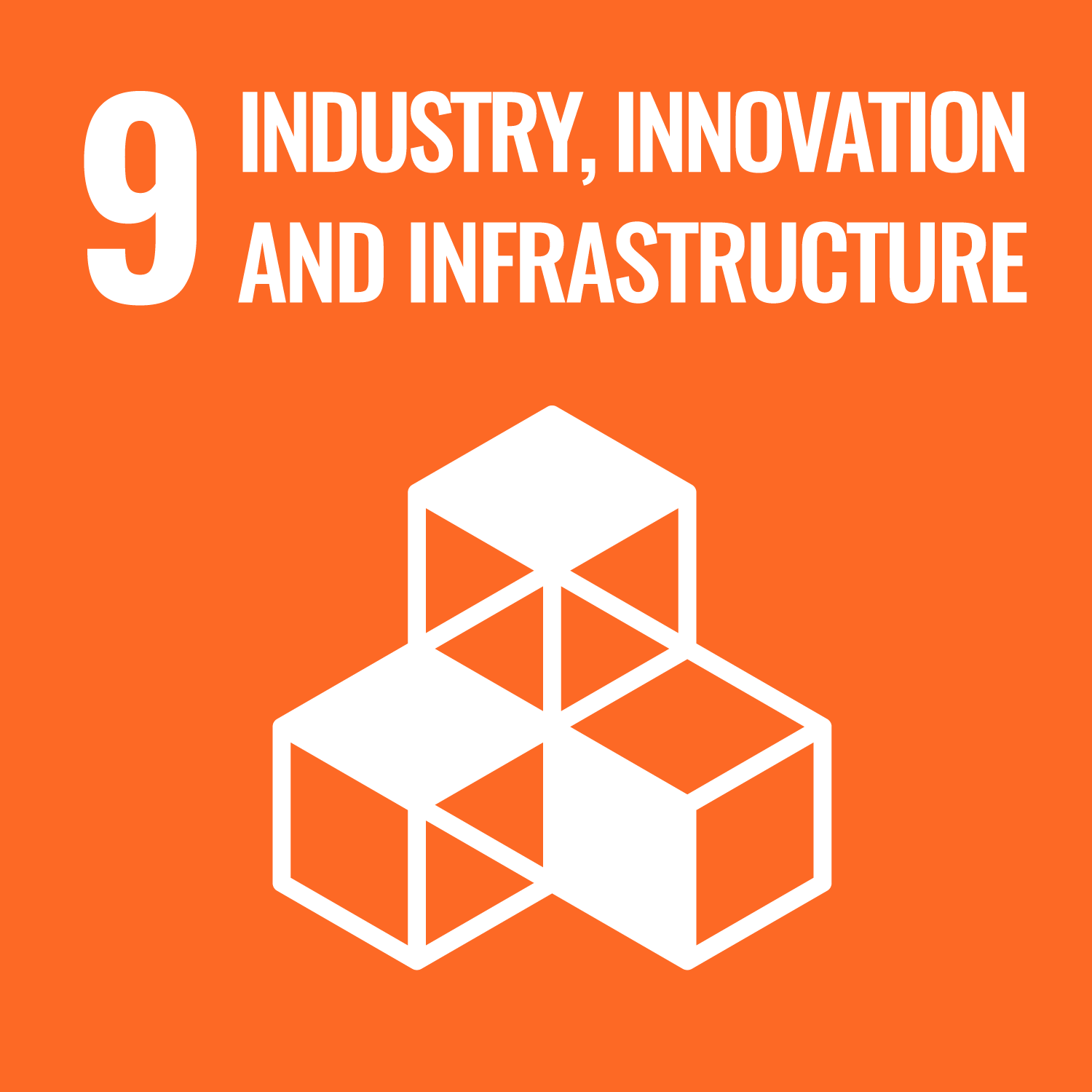